Maximizing Equipment Efficiency Through Packaging Machine Repair
Maximizing Equipment Efficiency Through Packaging Machine Repair
Blog Article
Quick and Reliable Packaging Machine Fixing Provider to Decrease Downtime
In the affordable landscape of manufacturing, the efficiency of product packaging operations rests on the reliability of equipment. Quick and trustworthy repair work solutions are crucial in reducing downtime, which can result in significant economic losses and operational troubles. Comprehending the importance of prompt interventions and the function of expert service technicians can change just how companies come close to maintenance and repair services. However, browsing the myriad alternatives available for fixing services can be difficult. What aspects should businesses think about to guarantee they are making the right selection for their operational requirements?
Importance of Timely Repair Works
Prompt repairs of packaging machines are essential for maintaining operational efficiency and reducing downtime. In the hectic atmosphere of production and packaging, also small malfunctions can bring about substantial hold-ups and efficiency losses. Dealing with issues promptly makes certain that machines run at their optimum capability, consequently protecting the flow of procedures.
Furthermore, regular and prompt maintenance can prevent the escalation of small troubles into major failures, which usually incur higher repair service expenses and longer downtimes. A positive approach to equipment repair service not only protects the honesty of the equipment but also boosts the total integrity of the manufacturing line.
Additionally, prompt fixings add to the long life of packaging machinery. Devices that are serviced promptly are less most likely to experience from excessive deterioration, allowing organizations to optimize their investments. This is especially crucial in markets where high-speed product packaging is vital, as the requirement for regular performance is extremely important.
Benefits of Reliable Solution Companies
Trustworthy company play a pivotal function in making certain the smooth operation of product packaging makers. Their know-how not only boosts the efficiency of repair services but also adds significantly to the durability of tools. Reliable provider are furnished with the technological knowledge and experience needed to detect concerns accurately and execute efficient options promptly. This reduces the risk of persisting troubles and guarantees that machines run at optimum efficiency levels.

In addition, a trusted company supplies comprehensive assistance, consisting of training and advice for team on equipment procedure and upkeep ideal techniques. This not just encourages workers however likewise cultivates a society of security and effectiveness within the organization. In general, the benefits of involving reliable service companies extend past prompt repair services, positively impacting the entire operational workflow of product packaging procedures.
Common Product Packaging Maker Problems
In the world of packaging procedures, numerous problems can compromise the performance and performance of makers. One common problem is mechanical failing, typically stemming from damage or insufficient maintenance. Components such as electric motors, belts, and gears might stop working, resulting in failures that halt production. One more common problem is misalignment, which can trigger jams and uneven product packaging, affecting item high quality and throughput.
Electrical troubles can also interrupt product packaging operations. Damaged wiring or malfunctioning sensors might result in unpredictable maker behavior, triggering hold-ups and increased browse around these guys operational expenses. In addition, software glitches can prevent the equipment's programming, causing functional inadequacies.
Inconsistent product flow is another vital concern. This can occur from variants in product weight, size, or shape, which may impact the maker's capacity to handle products precisely. Ultimately, not enough training of drivers can aggravate these problems, as untrained employees may not recognize early signs of breakdown or might abuse the devices.
Resolving these usual product packaging maker problems immediately is necessary to keeping efficiency and making sure a smooth operation. Regular inspections and proactive maintenance can significantly minimize these problems, promoting a reputable packaging setting.
Tips for Decreasing Downtime
To decrease downtime in packaging operations, applying a you can try these out positive maintenance strategy is crucial. Routinely scheduled upkeep checks can identify possible problems before they intensify, guaranteeing equipments run effectively. Developing a regimen that includes lubrication, calibration, and assessment of vital parts can dramatically lower the frequency of unexpected break downs.
Educating staff to run machinery appropriately and recognize very early caution signs of malfunction can likewise play a vital function. Empowering drivers with the knowledge to carry out fundamental troubleshooting can avoid minor issues from triggering major delays. Keeping an efficient supply of vital extra parts can quicken repair work, as waiting for components can lead to extended downtime.
In addition, documenting equipment efficiency and upkeep tasks can assist recognize patterns and recurrent issues, permitting targeted treatments. Including sophisticated monitoring modern technologies can supply real-time data, making it possible for anticipating maintenance and minimizing the threat of abrupt failures.
Lastly, fostering open communication between drivers and upkeep groups makes sure that any type of abnormalities are promptly reported and resolved. By taking these aggressive procedures, businesses can enhance operational efficiency and significantly reduce downtime in packaging processes.
Selecting the Right Repair Work Service
Choosing the suitable repair service for product packaging makers is an important decision that can considerably influence functional effectiveness. A well-chosen company makes certain that your equipment is repaired swiftly, effectively, and to the highest possible criteria. Begin by examining the supplier's experience with your certain kind of packaging tools. A service technician aware of your machinery can like it identify problems more properly and carry out services extra quickly.
Following, consider the company's track record. Looking for comments from various other companies within your sector can offer insights right into reliability and top quality. Certifications and partnerships with acknowledged tools makers can also suggest a dedication to excellence.
Furthermore, assess their reaction time and schedule. A provider that can supply prompt support decreases downtime and keeps production flow constant. It's also vital to inquire about guarantee and solution warranties, which can show the confidence the company has in their job.

Conclusion
In conclusion, the value of quick and reliable packaging equipment repair service services can not be overemphasized, as they play an important role in reducing downtime and ensuring functional efficiency. By focusing on timely repair services and selecting reputable company, organizations can successfully keep and attend to usual problems performance. Executing aggressive maintenance methods and purchasing staff training additional enhances the durability of product packaging machinery. Inevitably, a strategic technique to fix services promotes a much more durable manufacturing setting.
Prompt repair services of product packaging equipments are essential for maintaining operational effectiveness and minimizing downtime.Furthermore, timely repair work contribute to the durability of packaging machinery. In general, the benefits of involving reputable solution suppliers prolong past instant repair services, positively affecting the entire operational process of product packaging procedures.
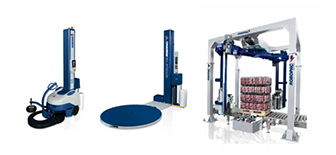
Report this page